The diameter of 1.4m rotary kiln tyre casting process
As we all know,rotary kiln tyre is also known as rotary kiln tire rolling circle, it is the main parts of rotary kiln device.Kiln tire is the full gravity of the cylinder (including gravity firebrick, internal devices and materials, etc.) to the roller, and the cylinder can be smoothly rotating the roller, so the tire have sufficient strength and durability; at the same time, the tire radial stiffness of the cylinder parts, and therefore it should ensure sufficient rigidity.
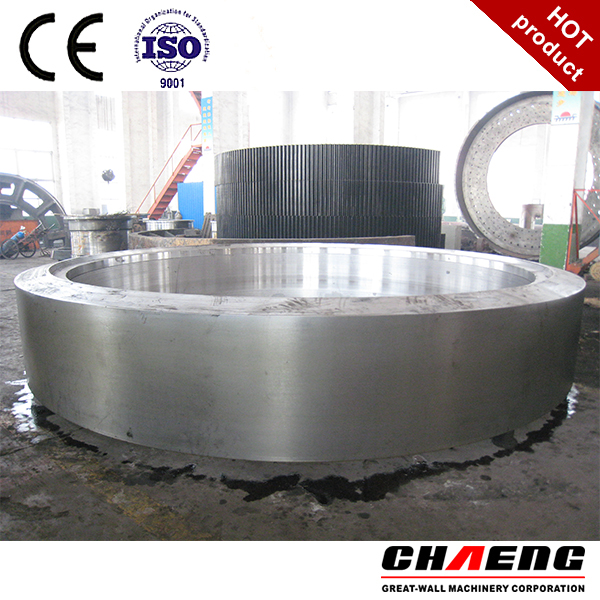
Casting Rotary Kiln Tyre Process Description
The first step: simulation, modeling
Prior to casting, the use of Chinese casting CAE software for digital simulation of the steel casting process, the process of forming products for process analysis and quality prediction, and tire casting process for continuous optimization. Complete sets of metallurgical aids Qi, the overall size of the control is good, water glass sand molding process, casting can prevent heat cracks occur while using pit modeling, not seasons, high production efficiency.
Step two: casting, heat treatment
The inspection of raw materials, in proportion into the electric arc furnace smelting, the molten iron sample spectral analysis, qualified in accordance with the "low-temperature fast pouring" the principles of casting, casting and recording time and temperature.
The third step: grinding, testing
Finally, cutting pouring riser, flash and so on. Great Wall has a professional polish steel finishing team, large-scale blasting equipment, can effectively improve tire appearance quality to the surface finish to meet customer requirements, and the use of advanced detection equipment testing for each wheel with NDT, to ensure internal quality, strictly eliminate any defective products factory.