Coal Mill Roller Cover
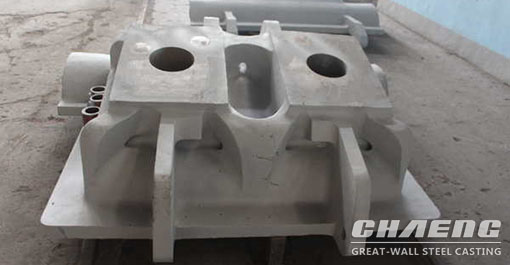
Weight : 3~20 t
Material :ASTM : A-27 70-40 / JIS: SCW480
Applicable device: coal mill parts
Application: Cement, electricity, metallurgy, chemical, non metallic mine and others
Customizable : Yes
Roller cover is an important part of coal mill. It is assembled with bearing block and grinder mill through the support of roller shaft and set on the outside of the door frame, equal to chassis. Turn up the roller cover when overhaul the grinder mill. The grinder mill manufactured by Great Wall Steel Casting adopts SCW480 material, which can guarantee the strength and toughness of roller cover. Japan’s famous manufacturer of coal mill introduces the roller cover of coal mill manufactured by Great Wall Steel Casting in the process of coal mill manufacturing, use performance of which is good.
Advantages:
I. Usage of computer technology
With the casting method of InteCAST and assumption of “instant filling, initial temperature uniformity”, analyze the numerical value and simulate the process of gradual solidification to design and optimize the process to achieve the purpose that prevent casting defects such as shrinkage porosity, shrinkage cavity and crack and meet inspection requirements.
2. Strict chemical composition and smelting control
Great Wall Steel Casting has a batch of professional technical engineers to make the mathematical statistics analysis. The study finds that each element has an influence on the solidification contraction, crack formation and service life of roller cover of coal roller mill. Thus, elementary composition of roller cover of coal mill shall be strictly controlled in the process of smelting to ensure the purity of molten steel.
3. Experienced casting team
Casting team of Great Wall Steel Casting constantly summarizes the experience and improve the technology during ten years of casting practice. Nowadays, a set of complete and effective principle formed in the process of casting, namely: insist the principle of low temperature and fast pouring, ensure the gradual increasing speed and solidification shrinkage requirement and improve the casting quality.
Our main material for the Coal mill roller cover is similar as followings:
Quality assurance:
The fabrication route is governed by the provisions of the implemented Quality System ISO 9001: 2000. The standard documentation ensures the full traceability of every process step:
• Manufacturer test certificates according to DIN EN 10.204 § 3.1 including chemical composition, mechanical properties and non-destructive examination;
• Dimensional check supported with a “as-built“ sketch;
• Record of the heat treatment chart;
Our service:
- Prompt response in 24h after your inquiry
- Several years high-precision processing experience
OEM service:
- Advanced management ability with high technology
- Strictly quality control
- We design the production according to your drawing when you supply the design drawing.
Roller Cover Manufacturing Process:
1. Wooden pattern Production
2. Molding
3. Pouring
4. First cleaning
5. Heat treatment – grinding (inspection)
6. Rough machining (inspection)-finishing machining (inspection)
7. Packing-delivering
Case:
After years of effort and development, steel castings manufactured by Great Wall Steel Casting have been sold to Henan, Hebei, Liaoning, Dalian, etc. In recent years, with excellent casting technology and high quality products, Great Wall Steel Casting attracts overseas people from Japan, South Korea and other countries to visit and inspect. Japan coal mill manufacturing enterprises designate Great Wall Steel Casting to provide all kinds of important parts for them, such as roller cover, bearing block, the support of roller shaft, shattered body frame, etc.