Ball mill hollow shaft and the cylinder end cap fracture reason
In normal operation,ball mills often encounter the mill hollow shaft coupling bolts and cylinder cover breakage phenomena, this failure repair inconvenient for everyday use and operation of the ball mill.
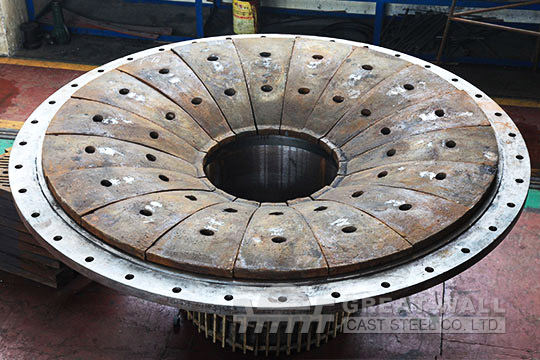
Nut clamping force attenuation cause loose bolts, and then complete loss of self-locking nut. The main reason nut clamping force decay are:
(1) thread gap is too large, poor self-locking performance;
(2) the pitch is too large, poor self-locking performance;
(3) threads roughness difference, by the force squeezed between the teeth increases the deduction pitch diameter with the gap back to shift the nut;
(4) the cylinder end cap surface is not machined surface roughness and flatness are poor;
(5) leading to the mill rotating nut loose;
(6) mill in operation, the grinding media and material impact on the cylinder body rotation caused some vibration mill, resulting in loosening of the nut.
Second, the way to deal with broken bolt
(1) improvement with a bolt and nut thread, so that thread diameter and top diameter and the smallest gap is zero;
(2) increase the thread surface roughness, the roughness should reach at least 1.6;
(3) it can not use thick thread, should be the appropriate choice of fine thread;
(4) mill shell thick cover should be based on the original 10mm thick; spigot depth dimension of the end cap can be reduced by 4 ~ 5mm in the original basis for further thickening in combination with the hollow shaft at within the thickness, while the inner cap is greater than the surrounding surface of the bolt head bolt hole diameter range Calibrating ensure that it is parallel to the outer surface of the hollow shaft.
(5) During use, periodically check the ball mill hollow shaft and end cover nut is loose, this is critical.