Introduction to high manganese steel jaw plate of jaw crusher
Moving jaw of jaw crusher is also called jaw head or jaw back. Jaw plate is also called toothed plate, which is the key wear-resistant part of jaw crusher. A set of jaw plate is usually composed of two parts, namely, the moving jaw plate and fixed jaw plate. Jaw plate is the major component of jaw crusher, including moving jaw plate and static jaw plate. There are different sizes according to the different types of jaw crusher, which generally use the material of high manganese steel.
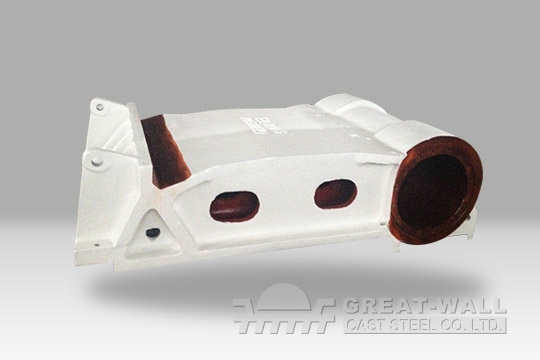
High manganese steel jaw plate
Materials used: Mn13, Mn13Cr2, Mn18Cr2 (namely super high manganese) or special dosing according to working conditions. Jaw plate of jaw crusher manufactured by Great Wall Steel Casting Company is exquisite with rigorous dosing and excellent heat treatment technology. Service life of jaw plate manufactured by our company is higher than 50% of that of the similar products.
Composite jaw plate
Cast by high performance new composite material, the service life of composite jaw plate is more than three times higher than that of ordinary jaw plate, which breaks the record that the service life of new material wear-resisting castings are only 1.5 times higher than that of manganese steel castings. Composite jaw plate, new composite rolling wall and so on transformed by scientific and technological achievement have been recognized by many industries with poor working conditions, such as mining industry and metallurgical industry.
Jaw crusher is used in many fields. Because of its different specification, feed particle size and hardness of materials, the extrusion and impact force to jaw plate is also different. Great Wall Steel Casting Co., Ltd manufactures jaw plates with various specifications and models by high manganese steel and metamorphic high manganese steel respectively to meet the need for jaw crusher in different working conditions.
Structure and features
1. Use manganese steel bonded carbide to make high wear-resisting degree and long service life.
2. Use cold hardening technology to make high hardness.
3. Carry out water toughening to avoid natural phase change in the use and leading to poor performance.
4. Strictly spot checked by laboratory and quality testing department before leaving the factory, so the quality of the product is assured.